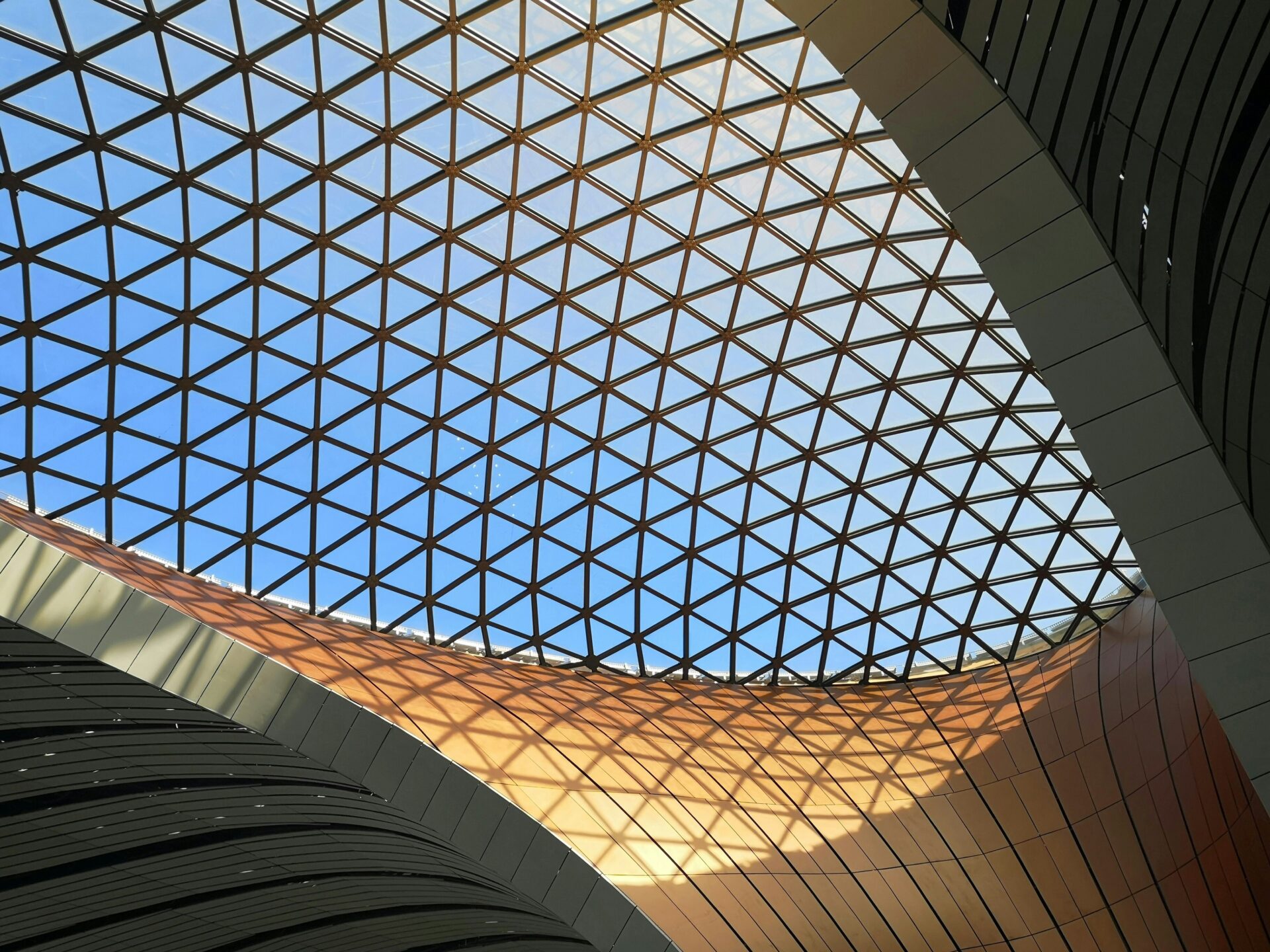
Technical project management: The underestimated success factor in industrial construction
Technical project management is a must-have for complex construction projects
If a client realizes early on that the multitude and complexity of project management tasks in industrial construction projects cannot be handled alone, it is a responsible and forward-looking step to call in external project management. In this article, we assume that the basic tasks of external project management are known. Let us briefly summarize them: External project management can take on all delegable tasks of the client - and in all five central areas of action: organization, quality, costs, deadlines and contracts (see our blog post: “Tasks of project management, project management and project control”)
Less well known - and unfortunately rarely actively offered on the market - is technical project management. In many projects, it remains in the background or is not considered at all. However, it is a decisive success factor, especially in highly complex construction projects, when it comes to meeting costs and deadlines.
What is the difference between normal and technical project management?
To our knowledge, there is no uniform legal or standardized definition for the term “technical project management”. The term describes a specific form of project coordination with a strong focus on the technical aspects of a project. Of course, ensuring that the technical project objectives are met is one of the basic tasks of the project manager. These include, for example
- Ensuring technical feasibility
- Checking and coordinating the plans of various trades/specialist planners
- Coordination of technical interfaces
- Monitoring technical milestones
- Evaluation of cost changes to technical systems
- Technical controlling
- Recognizing technical risks
- Identification of interfaces between process and building planning
- etc.
In short: normal project coordination primarily comprises organizational, commercial and legal tasks. Technical project management, on the other hand, focuses specifically on technical content and issues.
Problem interface: process <> building
Let's take a closer look at the interface between process and building: At this point, the potential for success or failure is highly weighted. The scope of services of architects and specialist planners is often limited to the basic services and possibly some special services according to HOAI. This almost inevitably results in an underweighting of the essential tasks at the interface between the process - i.e. what the company urgently needs due to its own objectives - and building planning. It is not part of the conventional planning team's remit to deal intensively with the company's process and in particular: its requirements. Nor can this be done with reference to service phase 1 of the HOAI. It is true that the client's specifications are collected in this phase. However, “collecting” does not mean “intensive examination of the company process”. The latter requires a much deeper immersion in the process-related interrelationships of the company and must be determined and defined by the company itself. This phase zero - as we like to call it internally - can be moderated and managed by a project coordinator.
Experienced project coordinators will make this their task as early as the project preparation phase, i.e. the phase before the conventional start of planning, and ask the company to think deeply about its own future process and workflow. This is sometimes a tiresome but unavoidable task for the company willing to invest. The result of this preliminary thinking is the specification for the planners - often in the form of process layouts, machine equipment lists, facility utility matrices, room books and more. Essential parts of these topics must be worked out before planning begins. The problem in practice is that this preliminary work is usually not done in sufficient depth during the project preparation phase. To be more precise, the topics are postponed until the planning phase.
The right tool for technical project management
Assuming that the planning team has been commissioned with a well-thought-out specification, the question arises as to what technical project management will look like in the future.
The main focus of technical project management is to verify the interactions between the building features and the processes and workflows. Reflecting highly complex requirements (e.g. in the semiconductor, aerospace or pharmaceutical industries), the momentum of the interplay between building and process becomes a success factor. Conversely, non-employment leads to failure to achieve the project goals. This sounds harsh, but it is often the case. The consequences are well known: In the worst case, it means dismantling; in any case, it means delays and additional costs, because what was previously neglected must now be made up for.
So how can a project coordinator proactively support the process? One tool we created ourselves over 20 years ago is the “eventmatrix©”. This works in a similar way to the now well-known fire incident control matrix. However, it is much more comprehensive and the primary events are not limited to fire incidents. In principle, all possible primary events are listed vertically. This starts with the failure events of the power supply, continues with fire events and all possible failure scenarios of the technical building services and ends with certain weather events. The special feature: Failure events that occur on the process side and require a “reaction” from the building are also listed under primary events.
The horizontal line of the matrix lists the TGA components. In addition, there are events such as “evacuation alarm” or messages to the various control systems (e.g. gas warning systems, supply systems, etc.). And here again the special feature: Process components, if they are functionally related to the building, are also listed here. An illustrative example is an electroplating bath, which requires the permanent extraction of EX air. So what must happen at this bath if the primary event “failure of the EX process air” occurs? Must there be a second process air supply? Does the chemical bath have to automatically switch to an intrinsically safe state?
These topics are inevitably dealt with through the eventmatrix©. In other words, working with the matrix mercilessly uncovers connections and deficits that would otherwise not have been recognized. If, for example, a mechanical smoke extraction system requires the creation of a supply air opening to compensate for the extracted smoky air, then the primary event “activation of the mechanical smoke extraction system” would be assigned the corresponding secondary event, “opening of a supply air opening” (e.g. through a hall door). However, it is also possible that the fire department only wants to initiate such processes manually. In this case, this is exactly what would appear in the eventmatrix© in the column with the heading “Hall door”. The eventmatrix© then creates the requirement for the planner to implement precisely this event dependency in the planning - taking into account the normative (e.g. requirements for functional integrity).
The experience of almost 30 years of project coordination shows that the eventmatrix© has reliably uncovered deficits. This is not an accusation against the planners, but rather an indication that a suitable tool is needed to identify problems, which helps to make the undoubtedly complex interrelationships manageable.
Why timing and moderation are crucial
When does it make sense to start working on the eventmatrix©?
In our experience, the preliminary planning of the MEP trades should essentially be completed, because then the MEP components that must be taken into account in the eventmatrix© are known. There are schematics, system descriptions, redundancy specifications, you know what needs backup power or may even need to be supplied without interruption. There is a server room concept and one for the passive IT structure. The basic requirements for the building management system are known. This is exactly when the first version of the eventmatrix© should be created, because its findings in turn generate planning tasks that must be taken into account in the course of the design planning.
Of course, TGA specialist planners can take over the creation and moderation of the matrix. However, due to the fact that it goes far beyond normal planning, it seems more sensible to assign this task to the project partner, who by nature must have this overall view anyway. We therefore see the task of technical project management as lying explicitly with the project coordination team.
Conclusion
When constructing complex industrial buildings, the success of the project depends to a large extent on the well-functioning interaction between the building and the process. If this does not work, the company's day-to-day business is restricted to the point where the investment is reconsidered.
Technical project management is indispensable for such projects. Properly executed with the appropriate tools, it guarantees success; it saves costs and time. Due to the overarching nature of the task, a professional project coordination office is the first port of call for such a task, provided it has the expertise to manage such projects.